Counterflow
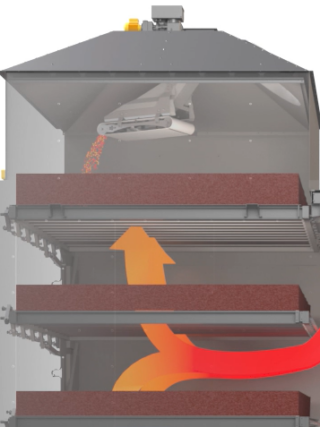
Dryers on gas or steam consume over 50% of the thermal energy used in an averageextrusion line. However, counterflow dryers offer a more efficient solution, saving both energy and plant space compared to other dryer types.
The vertical gravity flow design of counterflow dryers eliminates horizontal surfaces and minimizes the risk of cross-contamination and dust build-up. As a result, cleaning frequency is reduced, and cleaning is faster than with horizontal dryers.
Semi-continuous batch processing allows for quick changeover between different products without the need to wait for the dryer to be empty.
By uniformly exposing the product to warm drying air, counterflow dryers ensure high moisture uniformity. Additionally, the variation in product bed depth and number of drying beds allows for shorter or longer drying times..
When combined with a heat pump, counterflow recovery of heat from the exhaust air can reduce thermal energy usage by 60-75%. Partial or full electrification is possible, as well as a modular conversion from gas burners to heat pumps.
Counterflow Remote Diagnostics provides plant feedback to identify potential efficiency improvements.
Utilizing energy recovery and electric heat pumps for drying results in significant energy savings of 60-75% when compared to drying with gas or steam.
Geelen dryers are designed to operate continuously, 24/7, with minimal planned downtime for maintenance and cleaning.
Geelen offers solutions for full decarbonization of drying through the use of electricity, steam, hot water, biomethane, or hydrogen.