Inlet valve
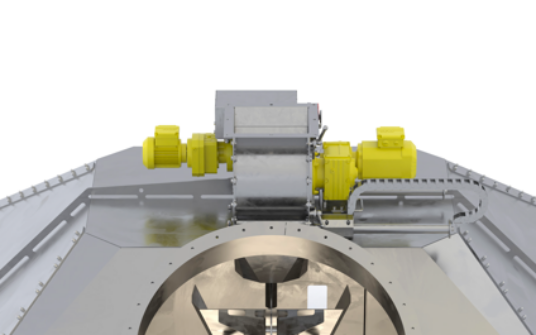
The founder of our company, Pierre Geelen, invented the counterflow cooler, which has become the global standard for cooling of feed and food products back to ambient temperature after steam conditioning, pelleting, extrusion, expansion or flaking.
Geelen Counterflow has installed over 10,000 units in more than 100 countries. We customize your cooler based on thousands of standardized components and offer five product groups of counterflow coolers, each with multiple sizes and a wide range of options.
The counterflow principle optimizes the use of cooling air, resulting in lower energy consumption, smaller space requirements and reduced maintenance.
PLC control of the cooling air volume ensures precise and uniform cooling, regardless of whether the cooler is full or almost empty. This feature also helps prevent condensation, which is critical for avoiding microbiological contamination.
The vertical gravity-flow process eliminates horizontal surfaces, reducing the risk of product build-up and cross-contamination.
Our process will remove almost all of the heat from your product, bringing it back to within 5 degrees Celsius of the ambient air temperature.
Counterflow coolers are known for being at least 30% more efficient in their heat exchange compared to horizontal coolers.
The efficiency of the counterflow cooler means that it requires at least 50% less space in the plant.